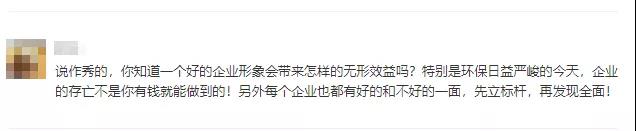



带着网友的疑问,水泥人网工作人员再次走进星级水泥磨房的所在地孟电水泥。星级水泥厂究竟是建造出来的,还是管理出来的?
企业相关负责人表示,星级水泥厂的打造不仅仅要靠造建设之初的用倾力打造,还要靠日常用心的维护保养。投入再多的资金购买再好的装备技术,也经不住日复一日,年复一年的磨损和消耗。
漏油的问题怎么解决?
据水泥人网了解,孟电水泥共有5条粉磨生产线,关键设备为Ф4.2×13m水泥磨机且全部配辊压机。其中1#2#3#4#四台辊压机配置8台减速机油站,每台油站配置1台回油泵回油,泵电机配置5.5KW,回油泵为CB-B200齿轮泵,四台辊压机共8台回油泵,用于减速机内油回流到油箱内。正常运行时供油温度34℃,运行时回油泵易坏油封易漏油,现场环境不好维持,给车间6S管理带来诸多困难,辊压机减速机回油泵技改势在必行。
↑↑↑技改前、
↑↑↑技改后
回油泵长期处于停用状态,现场漏油等环境问题得以彻底解决;回油泵长期处于停用状态,生产时节约4台电机4×5.5=22KW的运行功率,每小时节约电费22KW.h×0.59元=13
如此完美的效果,他们是怎么做到的呢?首先要设定技改的目的,制定具体的实施方案,预备所需要的材料做到有备无患,有的放失。
据企业负责人介绍,本次技改是通过彻底解决漏油造成的现场环境问题来达到改善环境节能降耗的最终目的。
现场工程师给出了具体的技改实施方案,在辊压机减速机回油出口出新增一个三通,原回油泵不拆除,在减速机回油出口处用Φ108钢丝橡胶管与回油泵到油箱的油管处连接,增加一个回油旁路。平时运行,让回油经旁路直接回油箱,不经过回油泵。回油泵在现场控制柜内新增一个3P空开,控制回油泵是的运行与否,在油温低、油流动性差时,启回油泵,油温高时,停回油泵。
漏油的问题就这样解决了!!仅用了108钢丝橡胶管2根4米,配两端法兰和3P空开2个。
冒灰、窜灰、外漏的问题怎么解决?
目前,在国内水泥粉磨行业中,测量称重仓料位大部分都采用称重传感器(如图1),
(图1)
作为测量料位的重要监测手段,称重仓在整个粉磨系统起着稳定辊压机电流、辊缝、压力的重要作用,常规的监测仓重手段是采用称重传感器,称重传感器的条件是进仓和出仓溜子位置必须是软连接,(如图2)
(图2)
用称重传感器监测仓重的弊端如下:
软连接会出现漏风或密封不严从而导致冒灰现象,并且经常出现软连接位置磨透冒灰,带来环保问题;软连接接口处特别容易卡料、积灰,造成软连接成“硬连接”从而导致仓重不准。另外称重仓是辊压机系统物料粉碎、热交换转接点,仓内产生蒸气、粉尘,对仓壁、仓顶粘贴严重。(如图3)
(图3)
称重仓内壁渍料会逐渐增厚,会造成称重数据与仓内实际有效物料偏差较大,会误导中控判断,从而引起仓满、入料提升压死等恶劣生产事故。
因传统称重传感器经常造成仓重测量数据偏差大、仓重变化波动较大,数据不可靠,经常需要人工介入测量:(如图4)
(图4)
人工在测量过程中有正压、蒸汽外冒等现象,不但会出现环保事件而且增加工人的劳动量和人身健康隐患。
就因为仓内物料热交换产生蒸汽、粉尘,且正压严重粘仓壁,仓上面的收尘管经常堵而无法采用其它方式测仓内料位,包括绳式、雷达、声波都接受不了仓内恶劣环境造成传感器粘结,因而常规测量数据参考性较差。
经过对现场环境分析,孟电水泥技术人员研发出了雷达监测+定时涡流喷吹、清灰装置,雷达传感器和仓顶渍料粘结问题得到解决:(如图5)
(图5)
将仓位传感器调整至0-5.5米,雷达波发射角度3°,雷达喷吹振打信号并联到磨机收尘器的某一室,当收尘器循环到这个室振打时,雷达喷吹振打同时工作,定时自动清理雷达与雷达发射通道粘料,确保雷达信号时刻保持畅通无阻、准确无误。
当磨机停运时,收尘器停运,喷吹振打跟着停运。经过试运,装在孟电2#水泥磨辊压机称重仓的雷达运行15天,效果良好,各环节不堵料不粘料,仓位误差0.1-0.2米,不用人工测量,数据可参考性较强。
目前,孟电水泥4台辊压机称重仓均安装了这种雷达料位计监测系统,原来的称重仓软连接全部封闭,杜绝了冒灰、窜灰、外漏等现象,既给生产提供了实时精确的仓位数据,又解决了人工测量带来的环保、人员健康等问题。
企业相关负责人表示,“企业不消灭污染,污染就消灭企业”,企业抓环保,越早越主动,越好!环保工作,只要认真、只要较真、只要动真,就没有解决不了的问题。这就是星级花园工厂的秘籍。